water vapour test for compressed air|Air Quality Standards ISO 8573.1 & ISO12500 : fabrication Compressed Air Testing Procedure for Water, Oil, and Particles . The use of properly calibrated hygrometers will help operators assess compressed air samples for water vapor in line with standard ISO 8573 . GARENA FREE FIRE. Diggy's Adventure. Murder in the Alps.
{plog:ftitle_list}
Resultado da CIBELLY FERREIRA. ALINE NOVAK. 😍 Conteúdo Amador. 🔥 Completo no GRUPO VIP. 👑 Conheça Nossos Grupos VIPs: 🔥 VIP 1 - OnlyFans e Privacy. .
Water Vapor Testing. This air testing method detects water vapor impurities in compressed air samples. The following methods utilize either the physical properties of water .Water Vapour, Condensed Water and Water Aerosols. Atmospheric air contains water vapour (water in a gaseous form). The ability of compressed air to hold water vapour is dependent . Desiccant dryers- using activated alumina- will adsorb water vapor from the air most effectively, delivering ISO 8573.1 Quality Class 2 (-40 ( F/-40 ( C) pressure dew point), ideal for the food processing industry. At this level of . Compressed Air Testing Procedure for Water, Oil, and Particles . The use of properly calibrated hygrometers will help operators assess compressed air samples for water vapor in line with standard ISO 8573 .
Water vapor vs liquid water in our compressed air We saw in the static example that the compressed air can hold 17 grams of water per cubic meter of compressed air. In total, we created 1,260 m³ of compressed air in a day. . While filters and water traps can eliminate most of the water vapor in compressed air, the most efficient means of moisture removal is using air dryers. . 7 August 2024 gas pipelines, hydrostatic testing, pipeline guide, pipeline testing, testing guide. Nitrogen Use in Metal Fabrication and Welding: Best Practices.
Water Vapor: Facilities can test for water vapor contamination using chemical reactor tubes. It is important to follow the manufacturer’s recommendations when testing with this media, but overall, it is a simple and inexpensive way .This moisture affects the whole system, including piping. Since hot, humid air has a higher moisture content than cold air, water vapor is created within the compressor. Consider a 55kW (75HP) rotary screw air compressor operating in a room with a 24 °C (75 °F) ambient temperature and 75% relative humidity.Ingested contaminants appear in the form of water vapour, hydrocarbon vapours, natural particles and airborne particulates. . We can conduct periodic compressed air purity testing at the point of use with certified results that can be measured against ISO: 8573-1 standards, testing for particle content, dew point and oil vapour concentration. .
The effects of water in air compressor system parts can be damaging, costly and corrosive. . as it indicates the temperature at which water vapor will condense into a liquid. To prevent this from happening, you must maintain a low dew point. . Timer-operated and zero-loss valves are usually equipped with test buttons. Look for this feature . If your recent air sample is not in compliance due to Water Vapor, this AirCheck Tech Note™ may help you identify the source of your Water Vapor contamination. A high Water Vapor reading may mean that the filter in the compressor has become saturated. When a filter cartridge becomes saturated it can no longer remove carbon monoxide and other .
2. Water/Water Vapor - Air contains moisture, which is drawn into the air compressor and enters the air stream as a vapor. As compressed air flows through the system, it cools, causing the vapor to condense in the facepiece or helmet. Moisture combines with oil and solid contaminants to form sludge, which can clog or damage system components.It is supplied complete with oil mist, water vapour CO and CO 2 test tubes to allow immediate multiple testing. In addition to the detection of compressed air contaminants listed above, the APTK1 also features an Oxygen Analyser allowing for constant real-time display of the oxygen content within the compressed air system. The APTK1 is not only . Proper air preparation significantly increases the process and production reliability of machines. Particles, water and oils in compressed air reduce the service life and functionality of components and systems. They also impair productivity and energy efficiency. In this article, a variety of air filtration and air treatment products are outlined and discussed, along with .
In general, compressed air testing is governed by ISO 8573. Depending on the application, additional standards such as USP, or NFPA, may apply. Testing Compressed Air/Gas Quality for Water. Water vapor (moisture) is a common issue in compressed air/gas systems, as the dewpoint of the air rises as the air becomes more pressurized. Water in . For the test conditions for the water content there are also particular characterstics (maximum 67ppm V/V for compressed gas cylinders or max. 870ppm V/V for compressed air generated by the compressor). The USP (the US Pharmacopoeia) handle the testing of water or oil content quite easily: the so-called mirror test is required. Water/Water Vapor - Air contains moisture, which is drawn into the air compressor and enters the air stream as a vapor. As compressed air flows through the system, it cools, causing the vapor to condense in the facepiece or helmet. Moisture combines with oil and solid contaminants to form sludge, which can clog or damage system components.
Compressed air, which is generated on site by pulling in ambient air and compressing it, contains water vapor, particulate matter (atmospheric air typically contains 140-150 million dirt particles/m 3). More importantly, the filtration systems that are employed are designed to protect process equipment from large slugs of water, oil, rust and .Water can be present in compressed air systems in two states: liquid and vapour. Liquid water usually consists of liquid aerosol and wall flow. . ISO 8573-3, Compressed air — Part 3: Test methods for measurement of humidity 3 Terms and definitions For the purposes of this document, the terms and definitions given in ISO 3857-1, ISO 5598 .When warm compressed air leaves the compressor it will contain a high moisture content in the form of water vapour. As the air travels through the compressed air distribution network it will begin to cool, and the water vapour will condense on cold surfaces it comes into contact with. The condensation can form in fittings and fixturesPractical Compressed Air/Gas Testing August 13, 2018 Technical Document TD-08- Rev 1 . 50˚F (67ppmv) depending on sensitivity of the product to water vapor. A dew point of 0 ˚F requires a refrigerated drier (Use TRI test item C23). A dew point of -50 ˚F requires a desiccant
All atmospheric air contains some water vapor which will begin to condense into liquid water when the air in a compressed air system cools to the saturation point, i.e., the point where it can hold no more water vapor. . wind tunnel air at high-testing velocities; these droplets may have the effect of machine gun bullets, tearing up the test .
the air compressor is also responsible for adding contamination of its own, making it contamination source number 2. Contaminants Added by the Air Compressor (Source 2) • Liquid Oil • Oil Aerosols • Oil Vapour (from compressor oil) • Wear particles Gaseous Ambient Contaminants Converted by the Air Compressor • Oil Vapour • Water VapourPressure in psi (gauge) Example - Water Extracted from an Air Compressor. Free air enters a compressor at atmospheric conditions 20 o C and 70% humidity ratio .The air leaves saturated at gauge pressure 8 bar and 40 o C .. Based on the diagram and table above the water content in saturated air entering the compressor can be estimated to be approximately 1.8 10-2 kg per .
The saturation point of water vapor in the air can be attained at ambient temperatures in some cases whereas, under other conditions, the air dew point might fall as low as 80°F or more below zero. . How to Measure Dew Point in Compressed Air. Accurate compressed air testing and dew point measurement is done using a specialized dew point . It utilizes hollow fiber membranes to remove water vapor from compressed air. The drying power of the membrane is controlled by varying the compressed air flow rate and pressure. SMC offers the IDG, Membrane Air Dryer Series (pictured), which can combine a mist separator and micro mist separator with a single unit.Compressed air — Part 5: Test methods for oil vapour and organic solvent content Air comprimé — Partie 5: Méthodes d'essai pour la teneur en vapeurs d'huile et en solvants . The sample shall be free from interfering contaminants, for example, water vapour, oil aerosol. The sampling and analysis of the oil vapour shall be performed using .
Compressed Air Testing – How to Test and Why It Matters
The amount of water that can be held in a volume of air is directly related to its temperature. Warmer air can hold more water vapor than cooler air. As air is cooled at constant pressure, it becomes more and more saturated. As the temperature continues to drop, excess water condenses as a liquid. The temperature at which this happens is the . Compressed air systems are the standard in various industries for their efficiency and reliability. However, one common issue pneumatic engineers may face is water in compressed air lines, causing many problems, including reduced system efficiency, corrosion, and equipment failure.If you've found yourself in this unfortunate circumstance, keep reading: .The new Dräger Oil Impactor was developed especially for the testing and checking of compressed air for oil aerosols. Apart from common and conventional oils, even synthetic oils can now be measured without problems – independent of their kind or viscosity – for the first time. . Water vapour; Close. Matching products. Product Order .
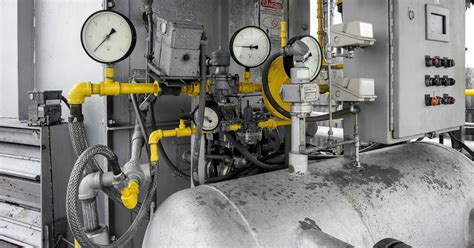
youtube tearing test
zelda tears of the kingdom sensor test
Resultado da Lotería de Boyacá: Últimos resultados, cómo jugar, sorteos y más. Desde el año 1923 la Lotería de Boyacá es una de las preferidas por los colombianos por ser una de .
water vapour test for compressed air|Air Quality Standards ISO 8573.1 & ISO12500